Music, maestro!
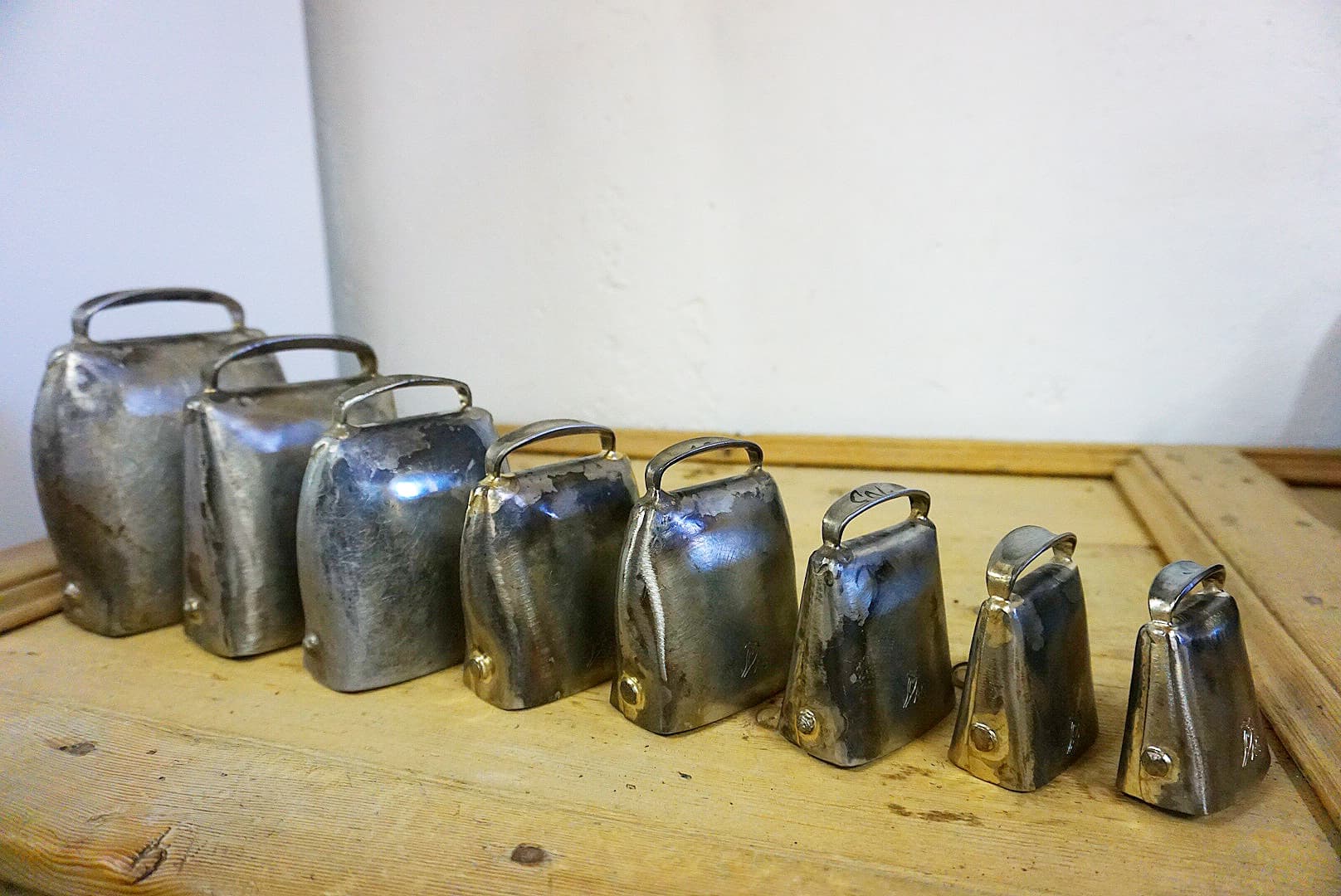
Like for the transhumance, the idyllic summer atmosphere in the malga (dairy farms) would not be the same without the sound of cowbells. The models change with respect to anniversaries: in addition to the ones used in the pastures, there are richly decorated bells for special occasions such as fairs, weddings or anniversaries. These are considered rare pieces and are cherished collector’s items. Alain Gamper, shepherd and bell smith originally from the village of San Nicolò in Val d’Ultimo, tells us about the art of making them.

For several years you have been specializing in the construction of bells: a family tradition?
No, I am self-taught, also because the master smiths rarely reveal their secrets. Although I was trained as a blacksmith, I must admit that initially it was not easy and the first attempts were unsuccessful to say the least. Then, slowly and thanks to my determination, I achieved my first successful results; now I also forge bells to order and for exhibitions.
How did you get the idea?
Since I have worked as a cowherd, I realized how essential it is to be able to recognize cows out of sight through the tolling of their bell, so as to always know where they are and what they are doing even in case of fog and above all without taking too many steps, since the territory is vast. In fact, a particular cowbell is assigned to the “herd leader” or to those who tend to move away from the group.
What elements make a bell “recognizable”, what determines its sound?
First of all, the handmade bells, as I and a few other craftsmen in South Tyrol create, are unique pieces and even the tone itself bears the author’s signature. Then, to make the sound higher or lower, it is the degree of hardness and the thickness of the sheet of metal, which they are made, as well as the quality and quantity of the alloy used to weld. I forge both silver alloy and brass plated wrought steel bells.
Does the shape make a difference?
Absolutely! There are flat, round and half-round models; the latter are, in my opinion, the best in terms of sound. In general, it is essential that the sound is clear, harmonious, full and audible even at a great distance.

What are the processing stages for forging a cowbell?
In the Tyrolean method, unlike the Swiss one, the bells are made from a single piece and not by welding two halves together. This means that Tyrolean bells, of the same size, weigh less: an aspect that should not be underestimated since the animals have to wear them around their necks for months. So, first of all, you cut out the shape from a sheet, according to the shape and size that the bell will have. Then it is modelled with an anvil and hammer, joining the two faces with a rivet (Niet) and beating well so that as little air as possible passes through. Two holes are then made to insert the bow (Hiag) where the clapper (Klachl) on one side and the collar on the other will be subsequently attached. Then we move on to brazing (Löten), which is a type of welding with the addition of filler material that has a melting temperature lower than the sheet itself, which is simply heated and not melted. This step is used to completely remove the air, otherwise the bell would not ring. At this point, it is necessary to clean and polish the bell, darkened by brazing, with special brushes and acids to give it a uniform appearance. As the very last step, also the most delicate and decisive one, the bell must be carefully tuned (Stimmen).
Having said this, it almost seems like the bell sings…
Sure, that’s exactly what it does. The bell has its own mouth, which is the lower opening, as well as a cavity: you can adjust its tone by adjusting the curvature of the lips or belly inwards or outwards, a bit like we open and close our mouth to pronounce lighter vowels such as “a” or deeper vowels such as “o”. Furthermore, bells, like people, have their own timbre of voice and must be mixed with wisdom and sensitivity to have a harmonious and inimitable proportion in the pasture.
Hence, assigning cowbells at the beginning of summer is like directing an orchestra, entrusting the instruments to the animals based on their character and predisposition. It must also be said that the sound, as much as the techniques for making cowbells, varies a bit like dialects: what is characteristic in one area and therefore considered the best, is perhaps disdained elsewhere.
